Saving Sight: The Toyota Effect
by Awl Sponsors
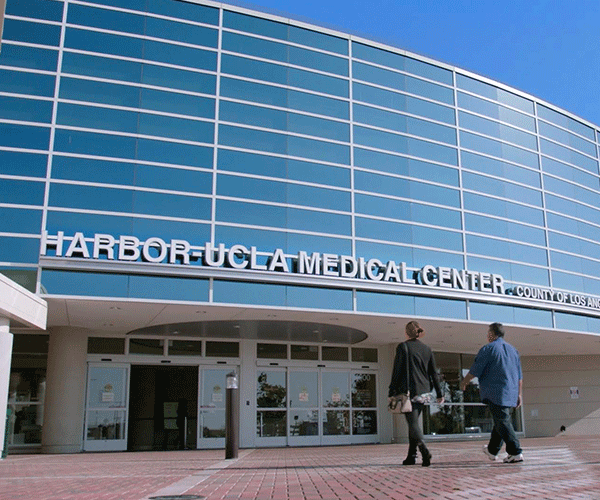
In business, it’s often the small things that have a big effect. And sometimes, innovation is as simple as sharing an idea.
Here’s something you may not be aware of: for over twenty years, Toyota — yes, the auto manufacturer — has been sending small teams to visit struggling businesses, with the aim of improving the efficiency and effectiveness of their operations.
Toyota developed a unique system, called the Toyota Production System, or TPS, that focuses on small, continuous improvements to drive high quality of work and competitiveness. These improvements run the gamut from improving social communication to process-oriented technology solutions. And they work for almost every company because the solutions are process oriented.
Sometimes, those solutions are as simple as color coded notes. This was the case with The Harbor-UCLA Medical Center — a county-owned medical facility whose mission is to serve the underserved. Before Toyota representatives came to share their knowledge, Harbor-UCLA had a surgical waitlist that was hundreds of patients long.
According to ChiefImprovementOfficer Susan Black, “When you work in chaos, it’s difficult to see what’s around you.”
Many patients, like Liseth — who required life-changing eye surgery that would prevent her from going blind — had to wait for months to receive the care they need.
So what does making cars have to do with hospitals and healthcare? According to Black, it’s about understanding the system you’re working within. “What TPS helped us do is see our own environment.”
After stepping back and watching the workflow of the hospital, Harbor-UCLA developed a color coded system that allowed patients waiting for different types of surgery to get taken care of more quickly. Over time the system yielded dramatic gains in efficiency — despite requiring only a simple change in organizational flow.
According to Black, “in general, early intervention yields better outcomes and requires fewer interventions.” Since her team is able to get to patients earlier and provide better treatments earlier, “we are able to get their medical conditions under control earlier.”
“Or better yet, are able to prevent major medical complications before they arise.”
Over the past two years, Harbor-UCLA has taken a surgical backlog that was over two-years long and practically eliminated it. Which means Liseth received the surgery that saved her eyesight.
Because TPS is a process-oriented approach, it can be applied to any hospital, fabricator, automotive company, or non-profit. It’s a method more than anything else that involves stepping back, analyzing workflow, and taking small, effective steps to fix deep problems.
For more stories of organizations that have benefited from TPS, , watch The Toyota Effect films here.
This post was created in partnership with Toyota. Opinions expressed do not necessarily reflect those of Toyota.